The Advantages of Insulated Concrete Forms Building Plans for Your Business
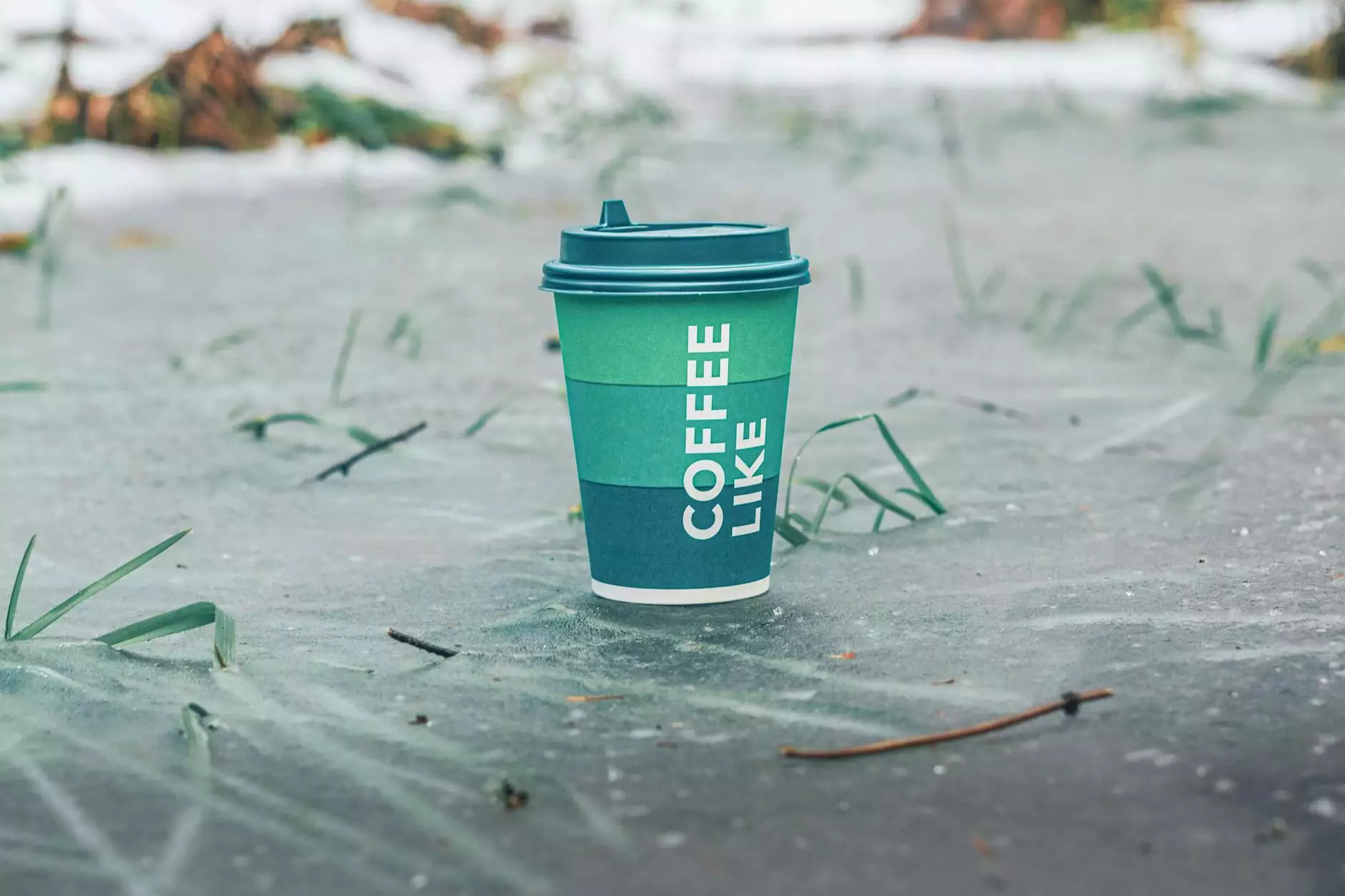
In the world of modern construction, insulated concrete forms building plans have emerged as a pivotal solution for architects, builders, and property developers alike. This innovative building technique offers numerous advantages, including enhanced energy efficiency, durability, and design flexibility. In this article, we will explore the various facets of insulated concrete forms (ICFs) and how they can revolutionize your construction projects.
What are Insulated Concrete Forms?
Insulated Concrete Forms (ICFs) are a construction system that consists of expanded polystyrene (EPS) foam blocks or panels that serve as a structure’s foundation. These blocks are easy to assemble, providing an insulated framework that is filled with concrete to create walls that are not only strong but also energy-efficient. The use of ICFs has gained popularity due to their unique combination of insulation and structural integrity, making them an excellent choice for both residential and commercial buildings.
The Key Benefits of Using ICFs in Construction
- Exceptional Energy Efficiency: Buildings constructed with ICFs offer superior thermal performance. The insulation provided by the foam forms reduces heat loss during winter and minimizes heat gain in summer, significantly lowering heating and cooling costs.
- Increased Durability: ICF structures are exceptionally resilient and can withstand harsh weather conditions, including high winds, hurricanes, and even earthquakes. This durability contributes to lower maintenance costs over the lifespan of the building.
- Speed of Construction: ICFs are lightweight and easy to handle. The panels can be quickly assembled on-site, allowing for faster construction timelines compared to traditional building methods.
- Soundproofing Qualities: The dense walls formed by ICF construction provide excellent sound insulation, making them ideal for commercial spaces like offices, hotels, and multi-family residences.
- Design Flexibility: ICFs can be easily cut and modified to achieve a variety of architectural designs, from simple rectangular structures to complex custom homes.
- Environmentally Friendly: Using ICFs can contribute to sustainable building practices, as they enhance energy efficiency and can include recycled materials.
The Construction Process of ICFs
Understanding how to effectively utilize insulated concrete forms in your building plans is crucial for maximizing their benefits. Below is a detailed overview of the ICF construction process:
1. Planning and Design
The first step involves drafting an ICF building plan. It's essential to work with an architect who understands the unique specifications of ICF construction. Factors such as load-bearing walls, window placements, and insulation thickness should be meticulously planned.
2. Purchasing Materials
Once your ICF plans are finalized, the next step is to source the necessary materials. Most ICF systems come with concrete, reinforcement steel, and foam forms. Brands like Fox Blocks, Nudura, and Amvic are reputable suppliers that offer high-quality ICF products.
3. Laying the Foundation
The construction process typically begins with laying the foundation. A standard concrete footer is required to support the ICF walls. This base must be level and solid, as it will carry the weight of the entire structure.
4. Assembling the ICF Walls
Once the foundation is prepared, the assembly of ICF walls can begin. The foam blocks are stacked and secured with ties. This assembly is both quick and efficient. Builders can adjust the height of the walls as needed, providing significant design flexibility.
5. Pouring Concrete
After the ICF walls are assembled, concrete is poured into the forms. The concrete fills the insulated shells, creating a strong, energy-efficient wall. Reinforcing steel bars can be added for additional structural support, especially in areas prone to natural disasters.
6. Finishing Touches
After the concrete has set, the forms can be removed. Finishing work, such as installing windows, doors, and additional insulation, can then be completed. The result is a robust, insulated structure that is ready for interior or exterior finishing.
Designing with ICFs: Best Practices
When integrating ICFs into your interior design plans, consider these best practices:
- Maximize Natural Light: Design large windows and skylights into your ICF structure to take advantage of the insulating properties while flooding interiors with natural light.
- Incorporate Energy-Efficient Systems: Use high-efficiency HVAC systems and energy-efficient lighting to complement the energy-saving benefits of ICFs.
- Focus on Aesthetic Appeal: Explore various finishing materials, such as stone or stucco, to enhance the visual appeal of the ICF structure.
- Space Planning: Utilize the strength of ICF walls to create open floor plans without the need for extensive internal support walls.
Costs and Financial Considerations
When evaluating insulated concrete forms building plans, cost is an essential factor. While ICFs may have a higher upfront material cost compared to traditional building methods, the long-term savings in utility bills and maintenance can offset the initial investment. Additionally, government incentives for energy-efficient construction may also apply, making ICFs an economically smart choice.
Challenges and Considerations
While ICFs offer numerous advantages, there are some challenges to consider:
- Initial Investment: As mentioned, ICFs can be more expensive to initially purchase. It's essential to consider your budget carefully.
- Construction Knowledge: Builders who are unfamiliar with ICF construction may need additional training or resources to ensure a quality build.
- Permitting and Codes: Always check local building codes and zoning laws to ensure compliance when planning your ICF project.
Conclusion: The Future of Construction with ICFs
Insulated concrete forms represent a modern, innovative approach to building construction. Their energy efficiency, durability, and design flexibility make them a superb choice for both commercial and residential projects. For companies like Fry Design Co., which focus on interior design, incorporating ICFs into your designs not only enhances aesthetic appeal but significantly reduces energy costs and maintenance requirements.
By considering insulated concrete forms building plans for your next construction project, you are not only investing in a structure that stands the test of time but also promoting sustainable building practices for a better future. Taking the step towards ICF construction is a decision that your business, your clients, and the planet will thank you for.