Die Casting Mould Supplier: Your Partner in Precision Metal Fabrication
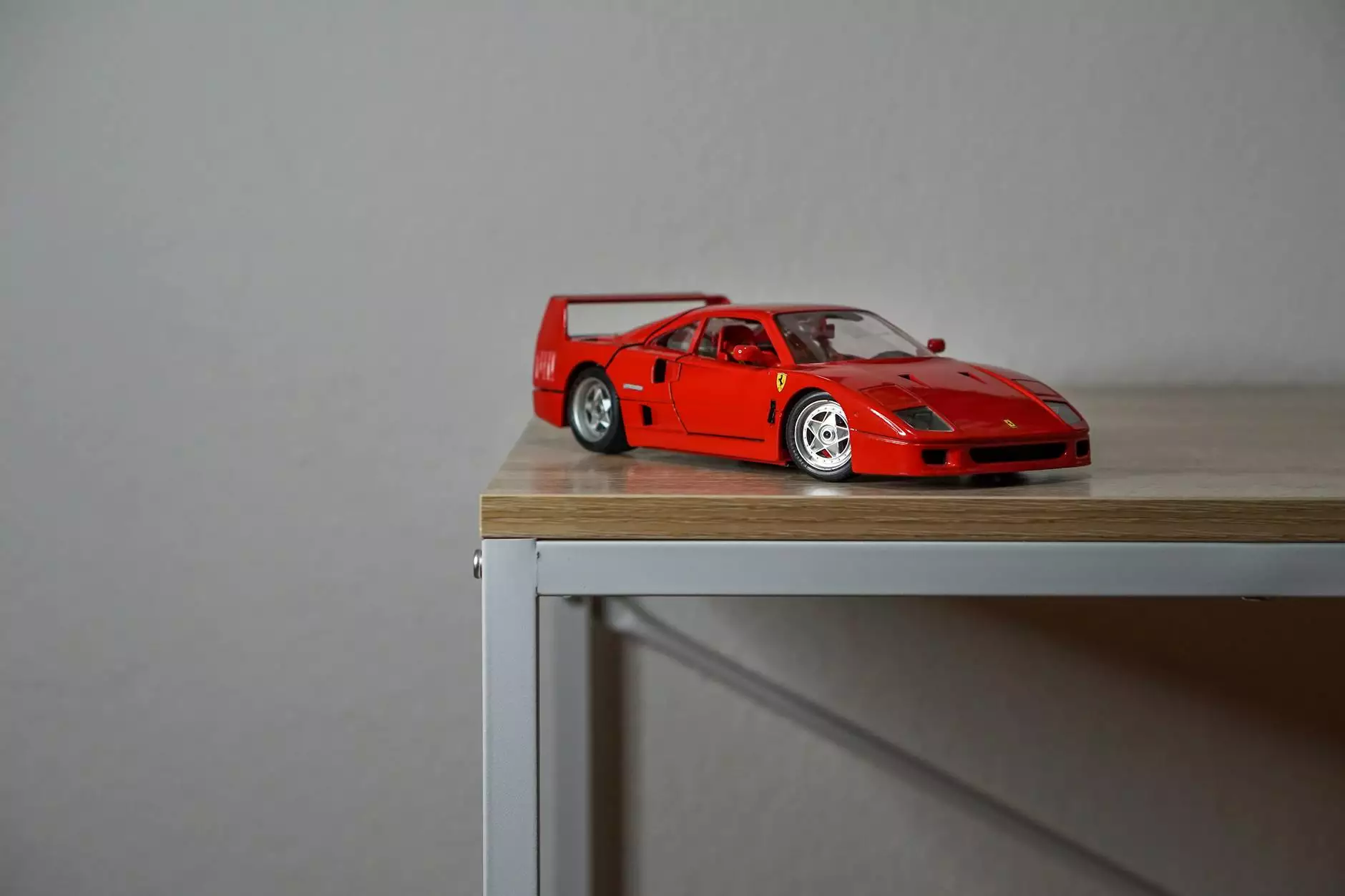
When it comes to the world of industrial manufacturing, the choice of the right die casting mould supplier can significantly influence the quality and efficiency of production. At Deep Mould, we take pride in being at the forefront of metal fabrication, offering cutting-edge solutions that cater to diverse industry needs.
Understanding Die Casting and Its Importance in Metal Fabrication
Die casting is a critical process used to produce metal parts with high precision and repeatability. It involves forcing molten metal into a mold cavity under high pressure, resulting in intricate shapes and fine details. This method is especially favored in industries requiring robust components, such as automotive, aerospace, and electronics. Here are some reasons why die casting is essential:
- Precision: Die casting ensures that each part is produced with remarkable accuracy, minimizing the need for additional machining.
- Durability: The metals used in this process tend to exhibit excellent mechanical properties, enhancing the lifespan of the components.
- Efficiency: With the ability to produce large quantities in a short timeframe, die casting is perfect for manufacturers looking to streamline their operations.
- Design Flexibility: Complex geometries can be achieved, allowing designers greater freedom to innovate.
Why Choose Deep Mould as Your Die Casting Mould Supplier?
Choosing the right die casting mould supplier can make a significant difference in your production line's efficiency and output quality. At Deep Mould, we are committed to meeting and exceeding our clients' expectations through:
1. Expertise in Metal Fabrication
Our team comprises highly skilled professionals with extensive experience in metal fabrication. We leverage advanced technology and methodologies to provide top-quality die casting moulds. Our knowledge of various metals allows us to recommend the best materials for your specific applications.
2. Diverse Range of Moulds
Deep Mould offers a vast array of die casting moulds suitable for various applications. Whether you need aluminium die casting moulds or zinc die casting moulds, we have you covered. Our versatile offerings cater to industries such as:
- Automotive
- Aerospace
- Electronics
- Medical equipment
- Consumer products
3. State-of-the-Art Manufacturing Facility
Our manufacturing facility is equipped with the latest technology, allowing us to produce high-quality moulds effectively. We utilize computer numerical control (CNC) machining and precision tooling techniques to ensure that each mould meets stringent quality standards.
4. Customisation Capability
At Deep Mould, we understand that each project is unique. That’s why we offer customizable solutions tailored to your specific requirements. Our team works closely with you to design moulds that align perfectly with your production goals.
The Die Casting Process: A Step-by-Step Overview
Understanding the die casting process can help clients appreciate the precision and care that goes into producing high-quality moulds. Here’s a detailed breakdown of how we manage the die casting process at Deep Mould:
1. Design Phase
Our process begins with collaborating with clients to design moulds that best suit their needs. We use advanced CAD software to create intricate designs and simulations to identify potential challenges early on.
2. Material Selection
Choosing the right metal for die casting is crucial. Common choices include:
- Aluminium: Lightweight and corrosion-resistant.
- Zinc: High strength and excellent durability.
- Magnesium: Offers a superior strength-to-weight ratio.
3. Tooling Production
Once the design is finalized, our manufacturing team fabricates the die casting tools. This involves machining components to create moulds that will perfectly shape the final product, ensuring precision and quality.
4. Die Casting Process
The die casting process itself can be broken down into several steps:
- Melting: Metal is melted in a furnace.
- Injection: The molten metal is injected into the mould under high pressure.
- Cooling: Once filled, the metal is allowed to cool and solidify.
- Ejection: The finished part is ejected from the mould.
5. Finishing Touches
After ejection, parts may undergo secondary processing for finishing, such as machining, polishing, and coating, to meet specific client requirements.
Quality Assurance: Commitment to Excellence
At Deep Mould, we adhere to strict quality assurance protocols to ensure that our die casting moulds produce flawless components consistently. Our quality control process includes:
- Material Testing: Ensuring that all raw materials meet industry standards.
- Process Monitoring: Continuous tracking during the production process to identify any deviations.
- Final Inspection: Comprehensive checks on moulds and products before delivery.
Cost-Effectiveness and Efficiency
One of the significant advantages of choosing Deep Mould as your die casting mould supplier is our ability to offer competitive pricing without compromising on quality. By optimizing our manufacturing processes and using advanced technology, we reduce waste and downtime, resulting in cost savings for our clients.
Environmental Responsibility in Metal Fabrication
As industry leaders, we recognize our responsibility toward the environment. Deep Mould is committed to sustainable practices in die casting. We implement:
- Recycling Programs: We recycle scrap metal and reduce waste.
- Energy Efficiency: Utilizing energy-efficient machines and techniques.
- Eco-friendly Materials: Sourcing materials that minimize environmental impact.
Customer Success Stories
Our dedication to excellence has allowed us to forge lasting partnerships with a multitude of clients. Here are some highlights from our success stories:
1. Automotive Innovation
A leading automotive manufacturer approached us for a custom die casting solution for a new electric vehicle component. By collaborating closely, we designed and produced a lightweight but durable mould that exceeded their performance expectations.
2. Aerospace Component Development
When tasked with creating complex parts for an aerospace application, our team utilized advanced simulations and precise manufacturing techniques to deliver a mould that met both the weight and safety requirements mandated by the industry.
Get Started with Deep Mould
If you’re looking for a reliable die casting mould supplier to enhance your production capabilities, look no further than Deep Mould. Our commitment to quality, efficiency, and customer satisfaction sets us apart in the metal fabrication industry. Contact us today to discuss your needs and discover how we can partner in your success.
Conclusion
Embracing the advantages of die casting can lead to significant innovations in metal fabrication. As your trusted die casting mould supplier, Deep Mould stands ready to support your business with unparalleled expertise and quality. Invest in the future of your production process and partner with us for all your die casting needs.